Technical Guide: Understanding Cosmetic Plastic Tube Manufacturing
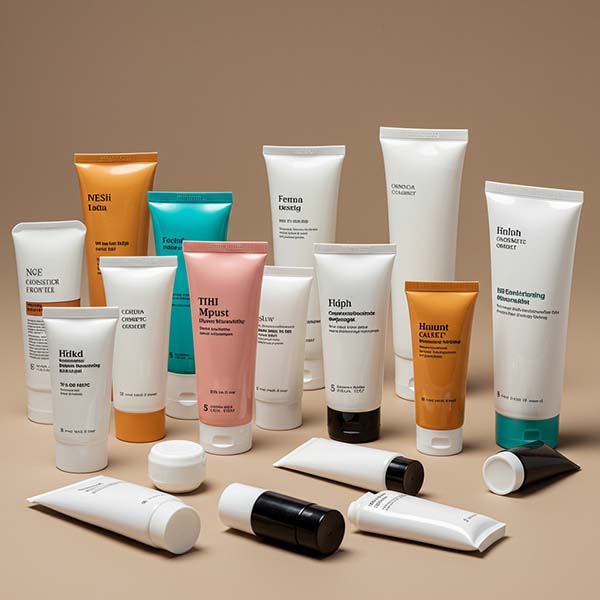
Cosmetic plastic tubes are a popular packaging choice for a wide range of products, from creams and lotions to gels and ointments. Understanding the manufacturing process is crucial for ensuring product quality and performance. This guide provides a technical overview of how cosmetic plastic tubes are made.
1. Extrusion
The process begins with plastic resin, typically polyethylene (PE) or polypropylene (PP), which is melted and formed into a continuous tube, known as a "sleeve." The thickness and diameter of the sleeve are precisely controlled to meet the product's specifications.
2. Heading
The continuous sleeve is cut into individual tube lengths. A heated mold is then used to form the head of the tube, including the nozzle and thread for the cap. This process is critical for ensuring a leak-proof seal.
3. Printing and Decoration
The tubes are decorated using various printing techniques, such as offset printing, silk-screen printing, or hot stamping. This step is essential for branding and product identification. A protective varnish is often applied to protect the artwork.
4. Capping and Sealing
Once decorated, the tubes are capped. The open end of the tube is then heat-sealed to create a secure closure. The type of seal can vary, from a simple flat seal to a custom-shaped seal.
5. Quality Control
Throughout the manufacturing process, tubes undergo rigorous quality control checks. This includes tests for leaks, print quality, dimensions, and material integrity to ensure that the final product meets the required standards.
Have Questions About Tube Manufacturing?
Our team of experts is here to help. Contact us for technical support or a custom quote.
Get in Touch